Decades of Excellence in Process Systems
Units & Automation Solutions
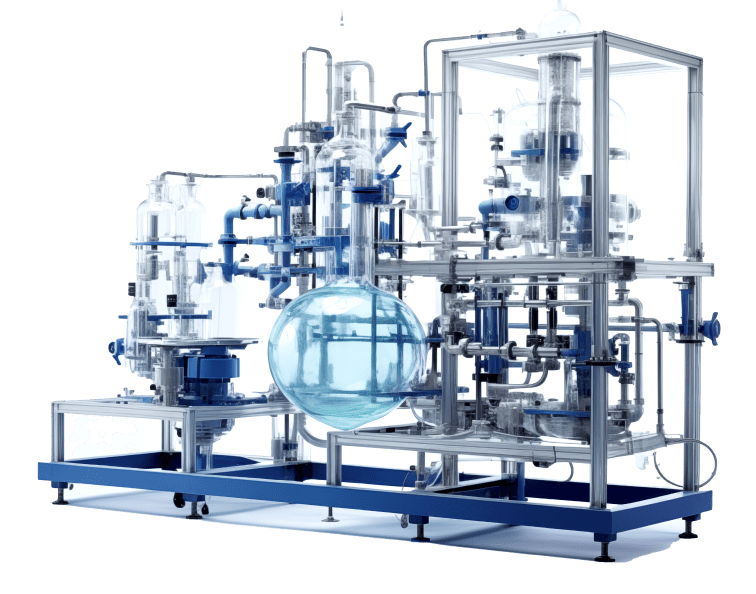
Decades of Excellence in Process Systems
Units & Automation Solutions
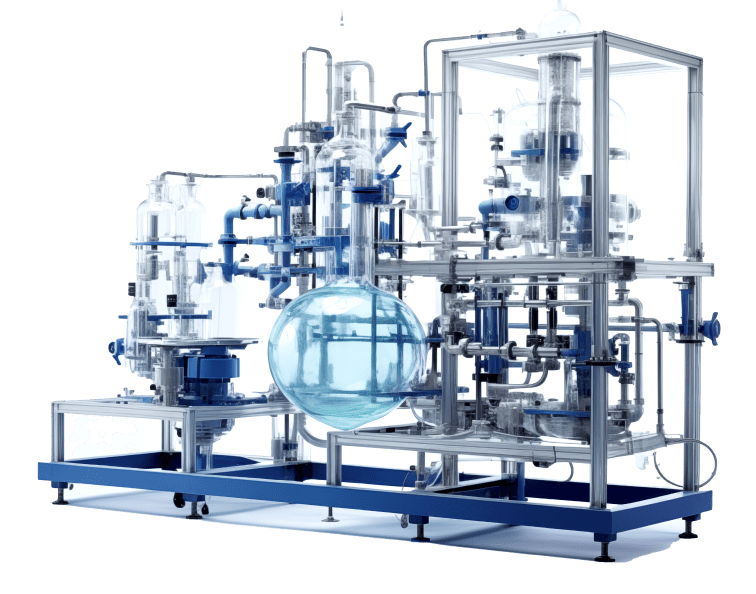
Decades of Excellence in Process Systems
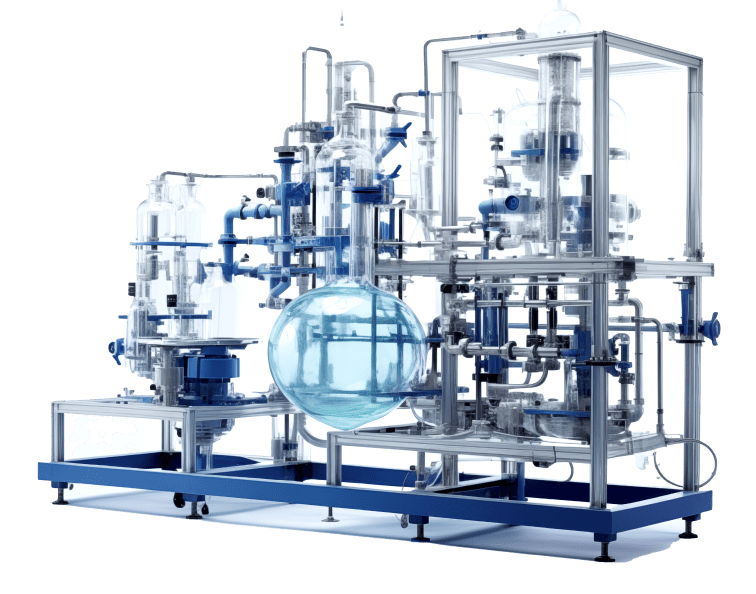
Trusted Leaders in Process Plants, Essential Oil Units & Automation Solutions
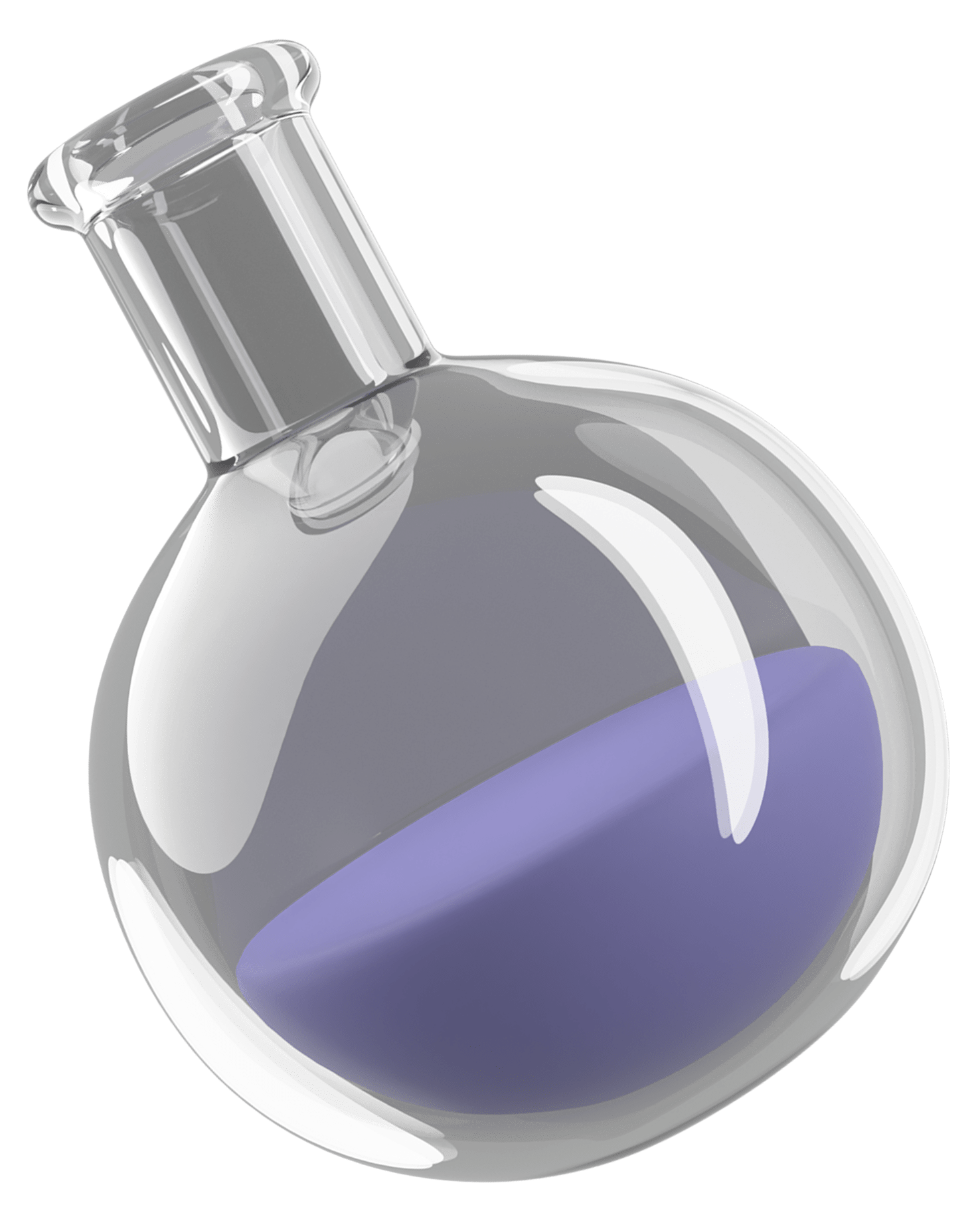
Who Are We?
We’re the industry leader in manufacturing and fabricating customized product ranges for our customers per their specifications. Owing to the excellent quality of our services and products, K-jhil has also attained the coveted memberships and affiliations from TUV & DAR.
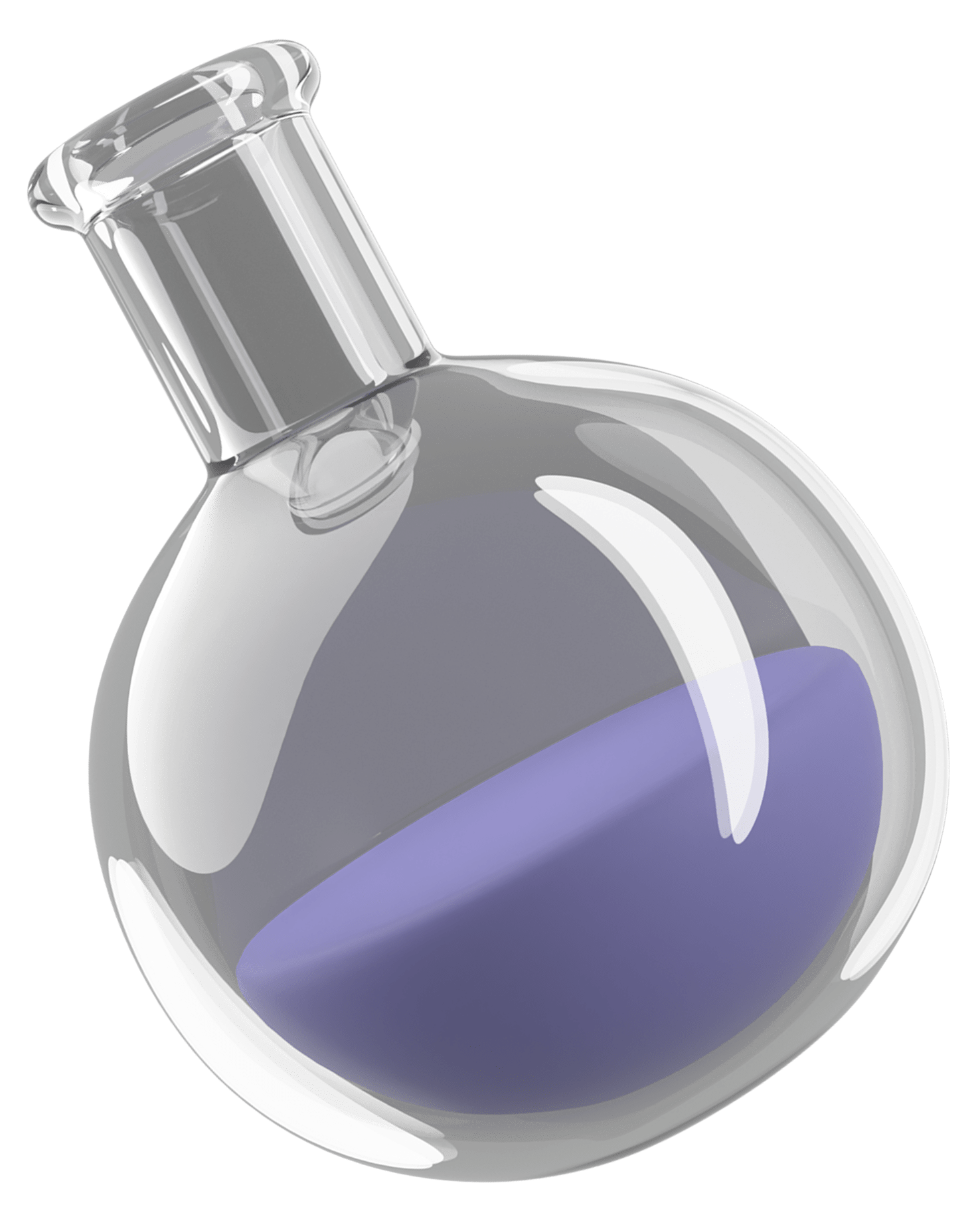
Who Are We?
We’re the industry leader in manufacturing and fabricating customized product ranges for our customers per their specifications. Owing to the excellent quality of our services and products, K-jhil has also attained the coveted memberships and affiliations from TUV & DAR.
Who Are We?
We’re the industry leader in manufacturing and fabricating customized product ranges for our customers per their specifications. Owing to the excellent quality of our services and products, K-jhil has also attained the coveted memberships and affiliations from TUV & DAR.
Our Products
High Performance & Technologically Advanced Chemical Process Systems
Our Products
High Performance & Technologically Advanced Chemical Process Systems
Our Products
High Performance & Technologically Advanced Chemical Process Systems
Manufacturing Excellence
Lorem Ipsum has been the industry’s standard
Manufacturing Excellence
Lorem Ipsum has been the industry’s standard
Our Clients
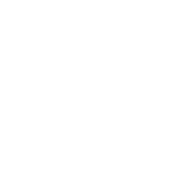
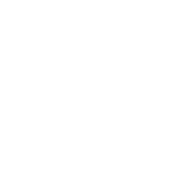
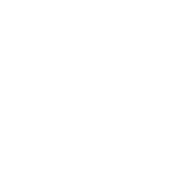
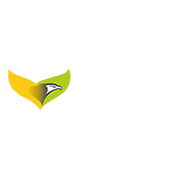
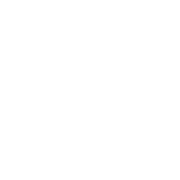
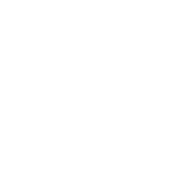
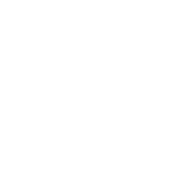
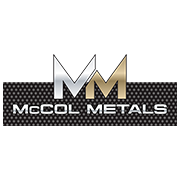
Our Clients
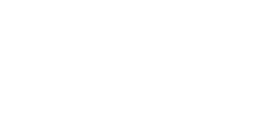
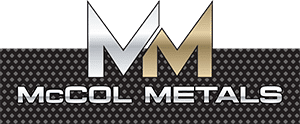
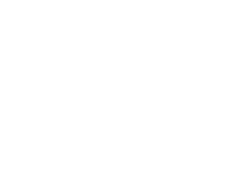
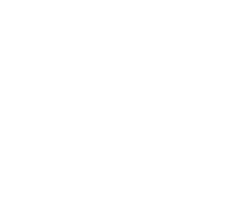
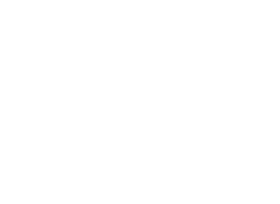
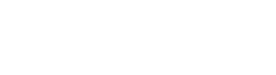
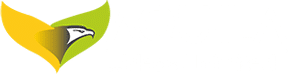

Request a Quote!
Request a Quote!
Fascinating Founding Story
1990
Humble Beginning
Manufacturing unit.
1995
Laying the Cornerstone of Excellence
K-Jhil found a place in Vapi GIDC and ventured into industrial equipment fabrication for the pharmaceutical and chemical industries.
2000-2018
New Feathers in Hat
Developing pilot plants for research and development, establishing a versatile laboratory, and revolutionizing thin film evaporators, bromine recovery, and HCL recovery.
2000
Expanding Our
Reach
Provided customers with package systems for different process systems, leading to potential revenue growth.
1997
Going Global with Our
First Export
Successfully exported a complete package system to the US.
2019 - Now
Taking over the World
Automation for Success: Embracing total automation in precious metal recovery plants for international projects.
Fascinating Founding Story
Establishing a small Glassware Manufacturing unit.
K-Jhil found a place in Vapi GIDC and ventured into industrial equipment fabrication for the pharmaceutical and chemical industries.
Developing pilot plants for research and development, establishing a versatile laboratory, and revolutionizing thin film evaporators, bromine recovery, and HCL recovery.
Provided customers with package systems for different process systems, leading to potential revenue growth.
Successfully exported a complete package system to the US.
Automation for Success: Embracing total automation in precious metal recovery plants for international projects.
Testimonials
Testimonials
Testimonials
FAQ’s
Lorem Ipsum is simply dummy text of the printing and typesetting industry. Lorem Ipsum has been the industry’s standard Lorem Ipsum is simply dummy text of the printing and typesetting industry. Lorem Ipsum has been the industry’s standard Lorem Ipsum is simply dummy text of the printing and typesetting industry. Lorem Ipsum has been the industry’s standard Lorem Ipsum
Lorem Ipsum is simply dummy text of the printing and typesetting industry. Lorem Ipsum has been the industry’s standard Lorem Ipsum is simply dummy text of the printing and typesetting industry. Lorem Ipsum has been the industry’s standard Lorem Ipsum is simply dummy text of the printing and typesetting industry. Lorem Ipsum has been the industry’s standard Lorem Ipsum
Lorem Ipsum is simply dummy text of the printing and typesetting industry. Lorem Ipsum has been the industry’s standard Lorem Ipsum is simply dummy text of the printing and typesetting industry. Lorem Ipsum has been the industry’s standard Lorem Ipsum is simply dummy text of the printing and typesetting industry. Lorem Ipsum has been the industry’s standard Lorem Ipsum
Lorem Ipsum is simply dummy text of the printing and typesetting industry. Lorem Ipsum has been the industry’s standard Lorem Ipsum is simply dummy text of the printing and typesetting industry. Lorem Ipsum has been the industry’s standard Lorem Ipsum is simply dummy text of the printing and typesetting industry. Lorem Ipsum has been the industry’s standard Lorem Ipsum
FAQ’s
Lorem Ipsum is simply dummy text of the printing and typesetting industry. Lorem Ipsum has been the industry’s standard Lorem Ipsum is simply dummy text of the printing and typesetting industry. Lorem Ipsum has been the industry’s standard Lorem Ipsum is simply dummy text of the printing and typesetting industry. Lorem Ipsum has been the industry’s standard Lorem Ipsum
Lorem Ipsum is simply dummy text of the printing and typesetting industry. Lorem Ipsum has been the industry’s standard Lorem Ipsum is simply dummy text of the printing and typesetting industry. Lorem Ipsum has been the industry’s standard Lorem Ipsum is simply dummy text of the printing and typesetting industry. Lorem Ipsum has been the industry’s standard Lorem Ipsum
Lorem Ipsum is simply dummy text of the printing and typesetting industry. Lorem Ipsum has been the industry’s standard Lorem Ipsum is simply dummy text of the printing and typesetting industry. Lorem Ipsum has been the industry’s standard Lorem Ipsum is simply dummy text of the printing and typesetting industry. Lorem Ipsum has been the industry’s standard Lorem Ipsum
Lorem Ipsum is simply dummy text of the printing and typesetting industry. Lorem Ipsum has been the industry’s standard Lorem Ipsum is simply dummy text of the printing and typesetting industry. Lorem Ipsum has been the industry’s standard Lorem Ipsum is simply dummy text of the printing and typesetting industry. Lorem Ipsum has been the industry’s standard Lorem Ipsum
FAQ’s
Lorem Ipsum is simply dummy text of the printing and typesetting industry. Lorem Ipsum has been the industry’s standard Lorem Ipsum is simply dummy text of the printing and typesetting industry. Lorem Ipsum has been the industry’s standard Lorem Ipsum is simply dummy text of the printing and typesetting industry. Lorem Ipsum has been the industry’s standard Lorem Ipsum
Lorem Ipsum is simply dummy text of the printing and typesetting industry. Lorem Ipsum has been the industry’s standard Lorem Ipsum is simply dummy text of the printing and typesetting industry. Lorem Ipsum has been the industry’s standard Lorem Ipsum is simply dummy text of the printing and typesetting industry. Lorem Ipsum has been the industry’s standard Lorem Ipsum
Lorem Ipsum is simply dummy text of the printing and typesetting industry. Lorem Ipsum has been the industry’s standard Lorem Ipsum is simply dummy text of the printing and typesetting industry. Lorem Ipsum has been the industry’s standard Lorem Ipsum is simply dummy text of the printing and typesetting industry. Lorem Ipsum has been the industry’s standard Lorem Ipsum
Lorem Ipsum is simply dummy text of the printing and typesetting industry. Lorem Ipsum has been the industry’s standard Lorem Ipsum is simply dummy text of the printing and typesetting industry. Lorem Ipsum has been the industry’s standard Lorem Ipsum is simply dummy text of the printing and typesetting industry. Lorem Ipsum has been the industry’s standard Lorem Ipsum
Product Catalogue
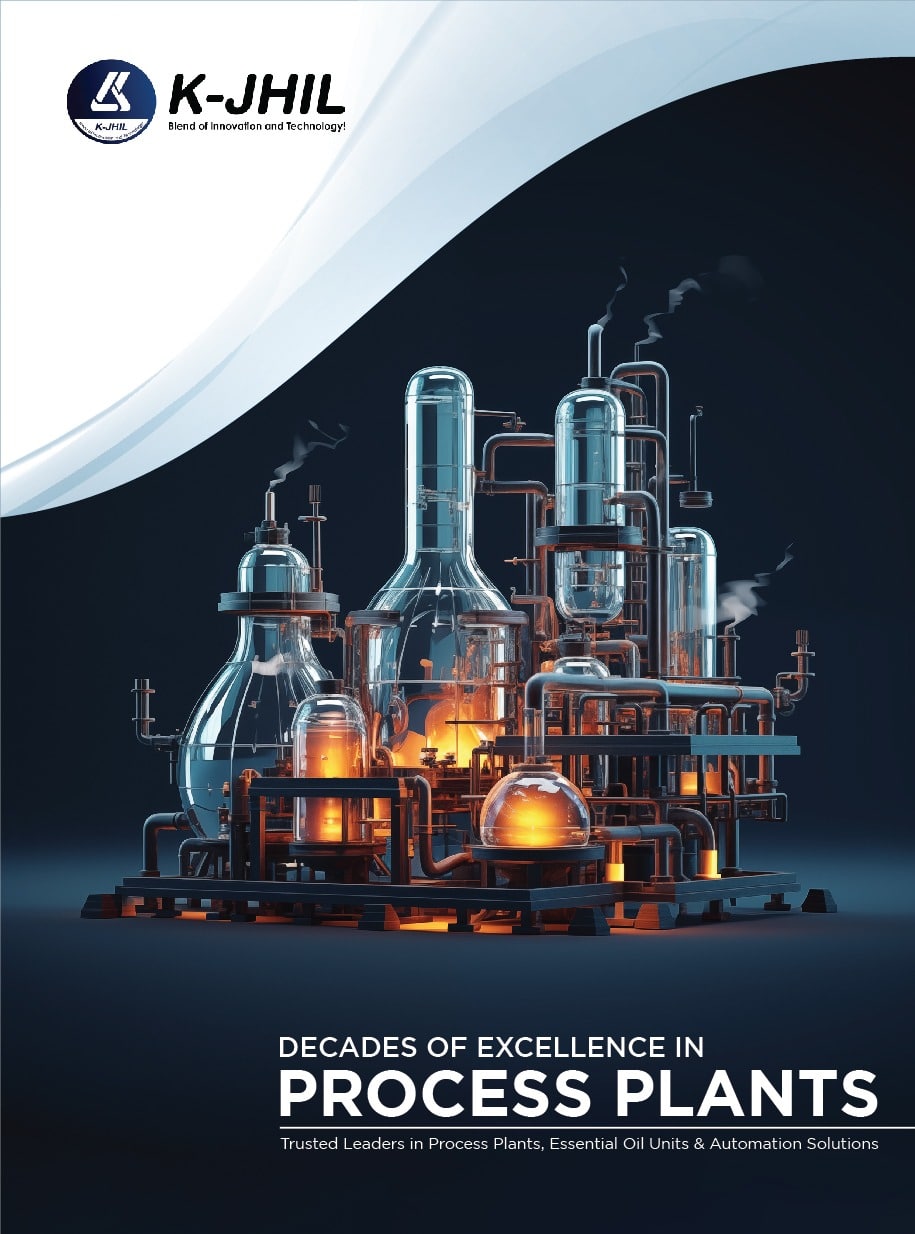
Download our Chemical Process System Product Catalogue to learn in detail about our products.
Product Catalogue
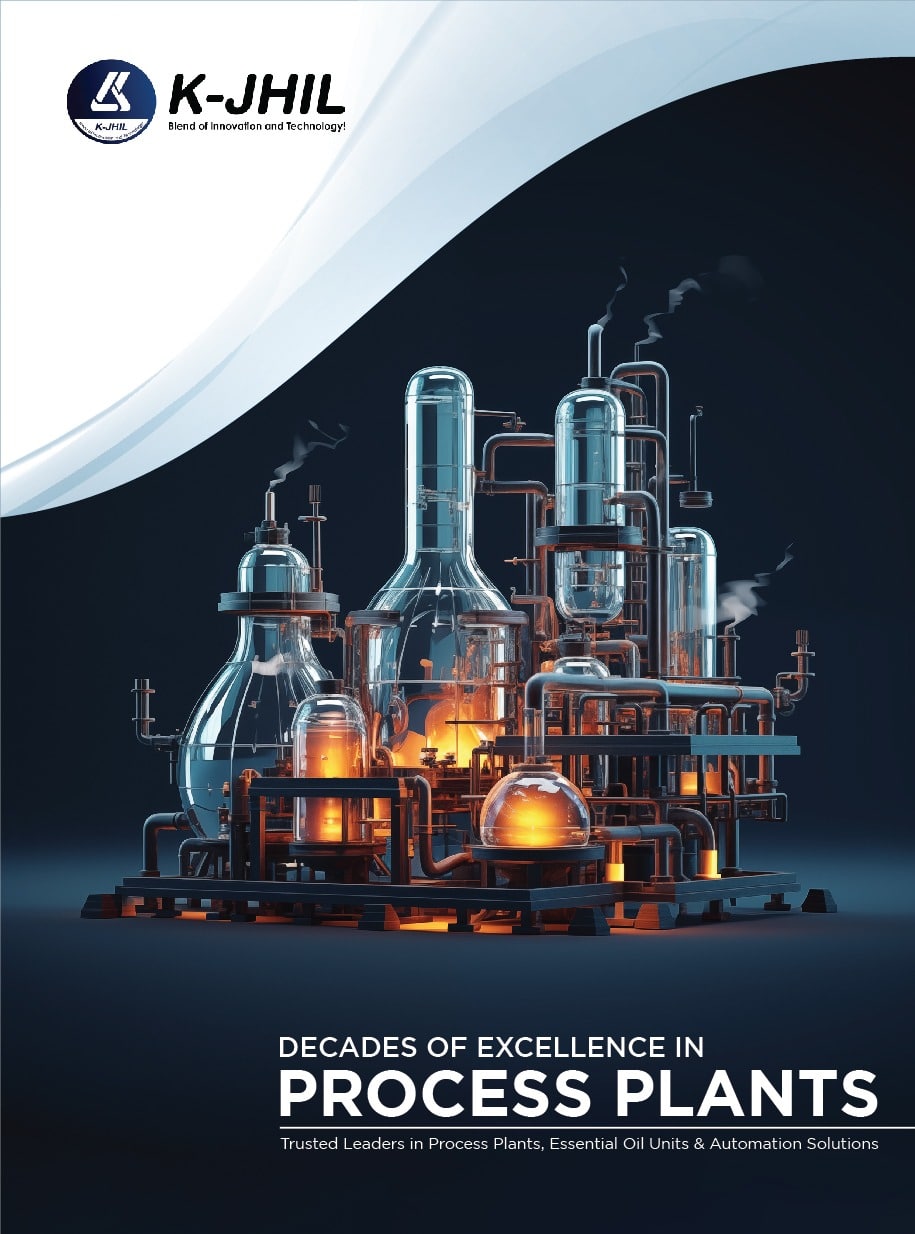
Download our Chemical Process System Product Catalogue to learn in detail about our products.